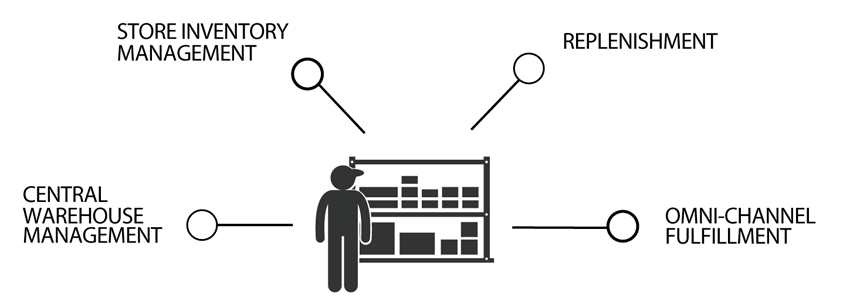
Inventory management challenges: omni-channel replenishment
As consumers start to simply expect a convenient omni-channel shopping experience, the use of alternative fulfillment options such as click-and-collect or same-day-delivery is on the constant rise. According to a survey conducted by Forrester Research in 2015, 42% of online shoppers already used click-and-collect. So the retail store will continue to be the hub of omni-channel fulfillment and customer engagement.
Since omni-channel consumers on average spend more and tend to buy additional items while they are picking up products, companies are inclined to constantly expand their respective service. This often is accompanied by an unprecedented visibility into retailers’ products, prices, locations and availabilities. Even real-time representation of stock levels at each individual location is getting a common and expected feature.
However this extensive customer centricity poses major challenges for logistics and therefore inventory management software.
Omni-channel poses new challenges for retailers' IT environments
The rise of in-store fulfillment in online shopping makes the optimal balance of product availability and storage costs more challenging. Without addressing replenishment, “save the sale at any cost” in an omni-channel environment leads to
- depletion of safety stock,
- degradation of in-store presentation
- and out-of-stocks at individual locations.
That creates a degradation of the in-store consumer experience, and sends a ripple effect into the supply chain by negatively impacting the accuracy of demand and seasonally adjusted store forecasts. So traditional logistic solutions are often rendered ineffective due to fluctuations driven by omni-channel demand. Ship-to-store rather than pull-from-store can help, but brings new challenges for costs and the supply chain in general.
Large retailers or entire industries, like the telecom sector, are responding with the introduction of new software that integrates omni-channel fulfillment, store inventory management, central warehouse management and replenishment to enable a continuous implementation of omni-channel processes. This allows for proactive and flexible responses to changing demand patterns at the level of the individual store.
Dynamic replenishment forecast
As part of the inventory management software, automated dynamic forecast calculations are therefore gaining in importance. These calculations are used to predict optimal order quantities during the replenishment process. Not only seasonal fluctuations are taken into account, but also relevant stock and sales data of each location. Key figures like minimum and maximum quantities for individual items at specific locations are then used to calculate the respective order quantities.
However, the retail sector will continue to experience further profound changes towards customer centric processes. As that change unfolds, the supply chain must react effectively to the consumer side. Only with the appropriate inventory management software, omni-channel customer centricity can be within the grasp of retailers.